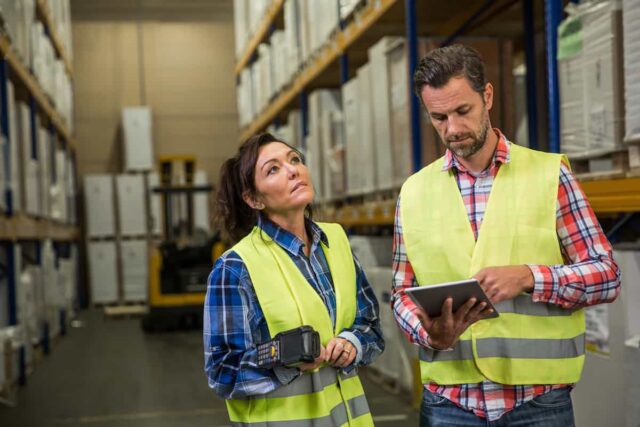
Inventory management is the backbone of the retail industry. It is the process of overseeing and controlling the storage, distribution, and flow of products within a retail operation. Effective inventory management allows businesses to minimize waste, reduce stockouts, and optimize the supply chain. In today’s highly competitive retail environment, accurate inventory management has become essential to success.
A key aspect of inventory management is ensuring that stock levels are accurately maintained, which requires precise counting and tracking of inventory items. One essential tool for achieving this accuracy is the counting scaleāa versatile and efficient device designed to simplify the process of inventory management. This article explores the role of counting scales in the retail industry, offering valuable insights into their benefits, applications, and potential impact on sustainability and environmental responsibility.
Overview
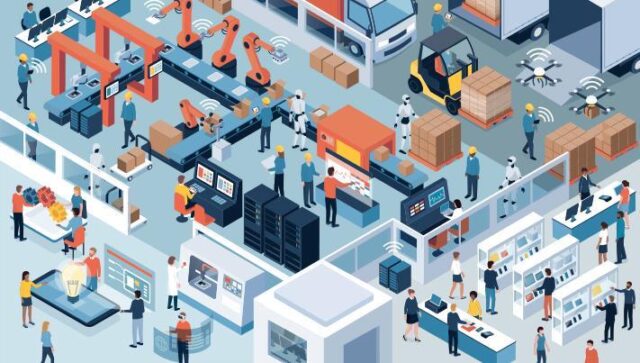
They are specialized weighing devices that combine the functions of weighing and counting into a single operation. They are designed to quickly and accurately count large quantities of small, uniform items, such as screws, bolts, or beads. In the retail industry, they are utilized for a wide range of applications, including counting stock items, managing inventory, and ensuring accurate pricing. It’s worth noting that businesses seeking to streamline their inventory management processes can benefit from specialized counting scales such as SWSCALE, which provides certified weighing and scale services for various applications, including truck, rail, and industrial use.
The role of counting scales in inventory management is to provide fast and accurate measurements of stock levels. By automating the counting process, these scales eliminate the need for manual counting, which can be time-consuming and prone to errors. As a result, counting scales help retailers maintain accurate inventory records, facilitating efficient replenishment, and reducing the risk of stockouts or overstocking.
The advantages
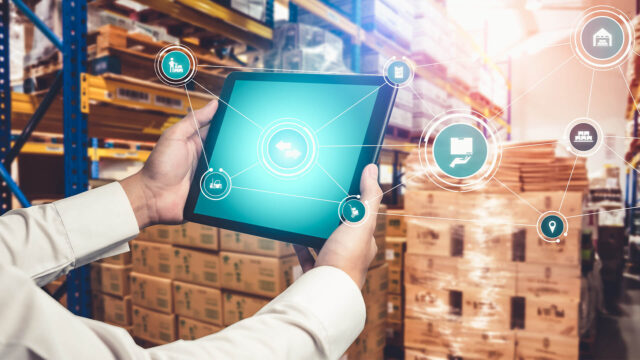
They offer numerous advantages for inventory management in the retail industry, including:
- Increased efficiency: They automate the counting process, enabling retailers to quickly and accurately determine stock levels. This saves time and labor, allowing employees to focus on other tasks and improving overall operational efficiency.
- Improved accuracy: Manual counting is prone to errors, which can lead to inaccurate inventory records and costly mistakes. They provide precise measurements, ensuring that stock levels are accurately maintained and reducing the risk of discrepancies.
- Enhanced profitability: Accurate inventory management is essential for maintaining optimal stock levels, which can help retailers avoid costly stockouts or overstocking. By streamlining the inventory management process, counting scales contribute to increased profitability and improved customer satisfaction.
Select the Appropriate Counting Scale
Selecting the right one for your retail operation involves considering several factors, including:
- Capacity: Choose one with a capacity that matches the largest batch size you expect to count. Overloading a scale can cause inaccurate measurements and potential damage to the device.
- Readability: Select a scale with a readability that meets your counting accuracy requirements. Higher readability indicates a more precise measurement, allowing for more accurate inventory management.
- Connectivity: Consider whether you need a scale that can connect to other devices, such as barcode scanners, printers, or inventory management software. This integration can streamline your inventory management process and improve overall efficiency.
- Durability and reliability: Look for a counting scale that is built to withstand the rigors of your retail environment, ensuring that it will provide accurate measurements over time.
Installation and Maintenance
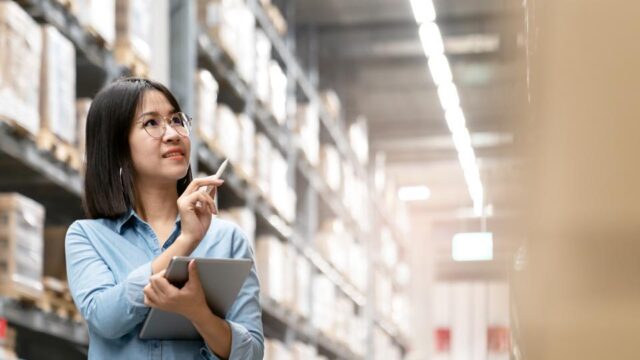
Proper installation and maintenance are crucial for ensuring the long-term accuracy and reliability of your counting scale. Consider the following steps:
- Installation: Choose a stable and level surface for your counting scale, away from direct sunlight, drafts, and vibrations that could affect measurements. Ensure that the scale is properly grounded and connected to a power source with an appropriate voltage.
- Regular cleaning: Keep it clean by regularly wiping it down with a damp cloth and mild detergent. Remove any debris or dust that may accumulate on the weighing platform and around the scale’s sensors.
- Calibration: Perform regular calibration checks to ensure your counting scale maintains its accuracy. This involves placing a known weight on the scale and adjusting it as necessary to match the known weight’s value. Consult the manufacturer’s guidelines for recommended calibration intervals and procedures.
- Preventative maintenance: Follow the manufacturer’s recommendations for routine maintenance, such as replacing worn or damaged components and lubricating moving parts. Schedule regular inspections to identify any potential issues before they become major problems.
The benefits
Integrating them into your retail management system offers several advantages, including:
- Streamlined inventory management: By connecting your counting scale to your inventory management software, you can automatically update stock levels, reducing manual data entry and minimizing the risk of errors.
- Enhanced reporting and analysis: Integrating them into your retail management system allows you to collect and analyze data on inventory levels, sales trends, and other key performance indicators. This data can be used to optimize inventory management strategies, leading to increased efficiency and profitability.
- Improved traceability: With an integrated retail management system, you can easily track the movement of inventory items throughout your supply chain, ensuring transparency and helping to maintain accurate inventory records.
Utilizing Data
To make the most of the data generated by counting scales, consider implementing the following strategies:
- Analyze sales trends: Use the data from it to identify patterns in sales, such as seasonal fluctuations or the popularity of specific products. This information can help you make informed decisions about inventory levels and product assortment.
- Optimize stock levels: By analyzing data from your counting scale, you can determine the optimal stock levels for different products, reducing the risk of stockouts or overstocking.
- Implement demand forecasting: Use historical data from your counting scale to predict future sales trends and adjust inventory levels accordingly.
- Monitor inventory turnover: Track the rate at which inventory items are sold and replaced, using this data to optimize your ordering and replenishment processes.
Conclusion
In conclusion, counting scales play a crucial role in the retail industry by providing accurate inventory management, which is essential for maintaining operational efficiency and profitability. The adoption of counting scales can lead to improved inventory accuracy, streamlined processes, and better resource utilization.
In the future, we can expect to see continued growth in the adoption of counting scales within the retail industry, as businesses increasingly recognize the value of these devices in achieving accurate inventory management and promoting sustainability. As technology continues to advance, we can also anticipate further improvements in the capabilities of counting scales, making them an even more essential tool for retailers seeking to optimize their operations and minimize their environmental impact.